As early as the 1996 Drupa exhibition, German KBA exhibited the world's first newspaper printing machine using shaftless transmission technology developed in cooperation with Bosch Rexroth, unveiling the development of the shaftless development of offset printing machinery. 16 years later, at 2012 Druba, KBA Germany debuted with the newly designed Rapida 106 and Rapida 145 sheetfed offset presses. The new design concept demonstrates that the German KBA is always on the shaftless transmission road. Unstoppable determination.
Shaftless transmission, also known as electronic shaft transmission or independent transmission, uses a direct drive motor to replace the original gear and shaft transmission system. This design brings many benefits to the printing machinery, making the design of the whole equipment easier, the system expansion easier, and also enhances the ease of operation of the equipment and reduces maintenance costs.
The new KBA Rapida 106 occupies the first printing speed of this format with a printing speed of 20,000 sheets per hour, and the preparation time of the job before printing just needs 3 minutes. Rapida 106 has achieved the printing task of 15 jobs in 500 sheets in one hour. This is also the only traditional offset printing equipment that can complete this printing task among many folios. The perfect closed-loop control and adjustment system, coupled with the large number of DriveTronic technology based on the shaftless drive, makes this device a new benchmark for sheet-fed offset printing equipment.
Shaftless technology reveals the secret of 3 minutes of pre-press preparation
With incomplete statistics, the highly automated KBA Rapida equipment uses shaftless drive technology on its feeder, paper feed, plate change, and various component cleaning devices to ensure that printing preparation time is minimized.
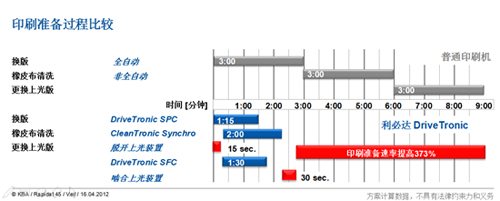
(The illustration of saving time before printing for KBA Rapida sheetfed offset printing machine and ordinary offset printing machine)
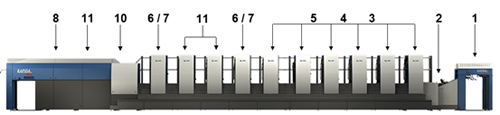
1.DriveTronic full preset feeder
This system achieves the least manual intervention and is fully automated. The system can use an automatic paper stack logic supply system and a fully automatic non-stop paper feed device. The entire paper stack can also be replaced at the highest speed.
2. DriveTronic SIS's unique sideless gauge feeder
The working principle of the paper feeding without side gauge is very simple. The position of the paper edge on the paper feed plate is monitored by two electronic eyes, and the data is transferred to the computer. The computer controls the gripper of the paper transfer roller. Before the printing cylinder, accurate positioning is performed.
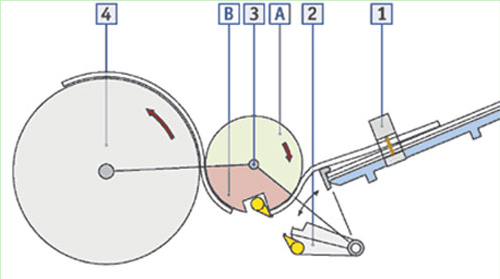
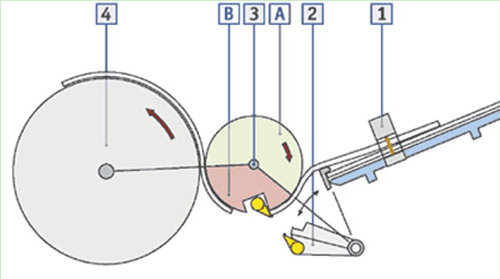
1. (paper) front-end detection sensor (Edge-detecting sensor)
2. Swing infeed
3. Single-revolution transfer drum
4. Impression cylinder A. Gripper bar lateral alignment phase B. Exact sheet-edge alignment phase
Drive Tronic SIS induction feed without side pull gauge does not require manual setting for adjusting the side pull gauge, thus avoiding some failures and waste due to manual adjustment. Because it avoids the error of paper connection, it has become an indispensable technology for KBA high-speed sheet-fed printing equipment.
3. DriveTronic SPC simultaneous automatic version change
The brand-new Drive Tronic SPC synchronous plate-changing device abandons the traditional transmission method connected by a gear clutch, but drives each plate cylinder by an independent motor. This individually driven plate cylinder technology is also the basis of the entire synchronous process.
Due to the operation of the independent motor, it is possible to allow the printing machine to perform the cleaning of the printing device and the glazing device while changing the plate, and this possibility can save the equipment up to 60% in the preparation time of the plate.
4. DriveTronic Plate Ident plate recognition
Drive Tronic PlateIdent printing plate recognition is to spray two-dimensional code on the printing plate when making the plate, and to pre-read the two-dimensional code on the printing machine to judge whether the printing plate is installed with the correct technology.
This set of plate recognition device has three major features:
1. Optical detection of the printing plate in the process of changing the plate; 2. Adopting pre-registration technology; 3. The authenticity of the printing plate can be checked using a QR code. If the printing plate is wrong, the machine can quickly identify and stop the activity.
PlateIdent plate recognition system has three major advantages:
1. Plate change monitoring through positioning pins, to achieve the detection of the plate during the plate change process, reliable plate change, less interruption 2. The pre-register function makes the registration correction completed before the first printing, and simplifies the printing preparation, reduces Attrition; 3. The detection of printing plate authenticity, printing components, color separation printing plates, and version language greatly reduces the risk factors of the printing calculation process.
5. CleanTronic Synchro synchronous cleaning device
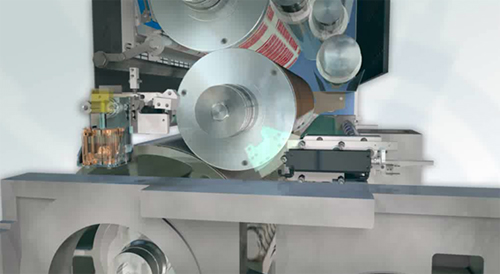
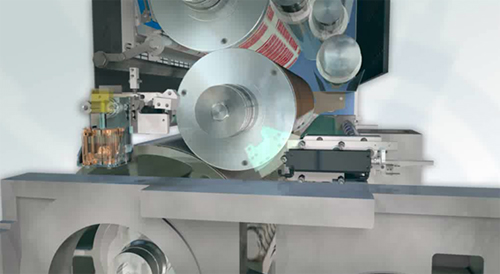
The advantage of KBA CleanTronic cleaning system is that it can simultaneously clean the ink roller and rubber cylinder, and no tools are needed during the cleaning process. As shown in the figure above, the cleaning rod on the right side is specifically used to clean the blanket cylinder, and the cleaning rod on the left side is swing type. It can clean both the rubber cylinder and the impression cylinder. If the cleaning rod on the left is also placed in the position of the cleaning blanket roller, the cleaning effect is increased by half, that is, the cleaning time is shortened by half. That is to say, there are two combinations of such a cleaning system: 1. When the left swing type cleaning rod and the right cleaning rod simultaneously clean the blanket cylinder, this combination is advantageous for commercial printing of folding cartons; 2. Synchronous cleaning of blankets The cylinder and impression cylinder are particularly advantageous for commercial printing.
Compared with the conventional cleaning device, CleanTronic cleans the impression cylinder and blanket cylinder at the same time, the plate is also replaced. In this way, the entire time including the three steps of replacing the printing plate, cleaning the blanket and the impression cylinder only takes 3-4 minutes, which can save about 50% of the time compared with the conventional design.
6. DriveTronic SFC synchronous polishing plate replacement
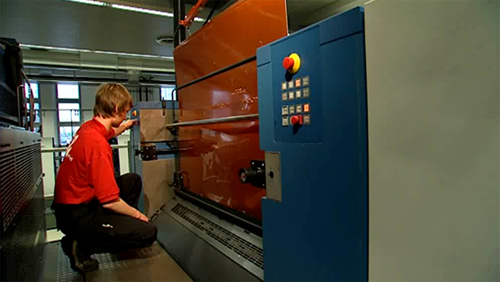
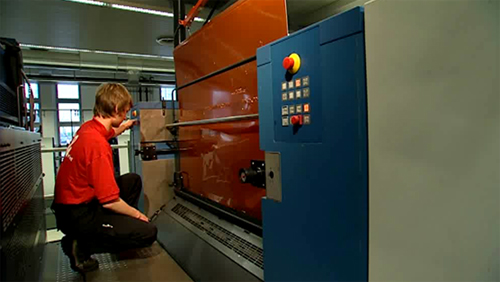
The automatic positioning roller, clamping plate and tension roller device of ordinary printing plates are used to reduce the replacement time period of the glazed plate to 1 minute and 30 seconds.
A small motor and a shaftless design concept. Since the birth of the first shaftless offset press, German KBA has been deeply involved in the shaftless transmission road. The printing equipment is faster, more stable and more automated without limits.
Basin Faucet,Single Level Basin Faucets,Single Hole Basin Faucets,Economic Stainless Steel Faucets
HESHAN ULA KITCHEN UTENSILS CO.,LTD , https://www.ulakitchenware.com