The main purpose of some brick factories to purchase coal quality analyzers is to test the level of coal heat generation (commonly known as large card count) to control the quality of coal intake; another purpose is to test the number of large internal combustion of bricks. The coal quality testing equipment is configured according to the above two requirements. Generally: four automatic testing equipment for automatic calorimeter, electric drying oven, electronic balance and micro sample preparation machine. According to the experience of Hebi Yongxin Electronic Installation Brick Factory coal quality testing instrument, the following is summarized as follows: building material factory brick billet internal combustion heat value measuring instrument
First, receiving goods inventory instruments and accessories
1. Instrument inventory: The brick factory only performs heat generation, and the configuration is generally; the automatic calorimeter, drying oven, electronic balance, and sample preparation machine are divided into three pieces. The automatic calorimeter main unit, sample preparation machine and accessories are combined one by one, the drying box is one piece, and the electronic balance is one piece.
2, room selection: not open, can not have no wind wall, can not be in the brick kiln and the distance of the room. It is recommended to choose a room with a relatively good office environment. The best rooms in Chongqing, Wuhan, Nanjing, Shijiazhuang and other hot summer areas are air-conditioned.
3, room power: four pieces of coal quality testing equipment are all 220V socket, the total power is less than 1.5 kW, so it is not necessary to separate the line, the general lighting is connected to a 2 kW high power plug.
4, room configuration: a stable level of the table, an oxygen cylinder, with 3 cylinders of purified water or 40L of distilled water in advance. Machine used by brick factories to measure calorific value
Second, the installation of laboratory equipment
Calorimeter installation
Note: First of all, check the inner cylinder of the calorimeter and its surface for debris, such as packaging debris, etc., must be cleaned first to prevent the pump from being blocked when adding water.
1. Open the calorimeter packing box and place the calorimeter on a flat ground (vertical) table to keep it steady and not shaken. Place the balance as far as possible on the countertop that is not to be shaken. It is best to be on the concrete countertop. Open the box and find the power cord plugged into the socket on the back of the calorimeter and connect to the 220V power supply.
2. Turn on the calorimeter switch, click “Settingsâ€---click “8†to test---click “Drainage Testâ€.
3. Open the inner cylinder cover of the calorimeter, and then continuously inject the inner cylinder into the pure water until the water overflows behind the calorimeter and stop the water injection. (Note that the water injection process is prevented from spilling onto the surface of the calorimeter so that water may enter the back of the main board. A towel can be placed in front of the inner tube.)
4. Click “Resetâ€----Turn off the power switch-----wipe the water at the edge of the inner tube of the calorimeter. Brick heat
5. Install the oxygen pressure gauge correctly on the oxygen cylinder. (First observe the oxygen cylinder outlet, whether the pressure reducer air inlet and outlet are dirty, should be cleaned to prevent damage and block the pressure reducer) Connect one end of the plastic gas pipe to the oxygen pressure gauge and fasten it. The other end of the trachea is attached to the oxygenator and is slightly tightened.
6. Screw the decompression screw into the pressure gauge and adjust 3.0 MPa.
7. Locate the oxygen bomb on the countertop that can be filled with oxygen. Compress the oxygenator chuck---insert into the oxygen warhead----release the chuck-----take the middle of the oxygenator Pull up-----I feel the card stuck after death-----Open the oxygenator brake switch for oxygenation for 30 seconds-----
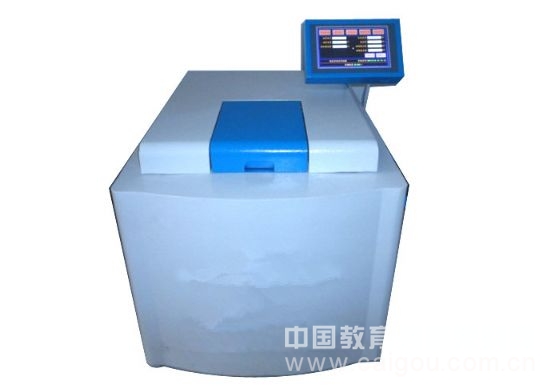
Valve Spare Parts
Valve spare parts including body, bonnet, yoke, disc, seat, ball, retainer, stem, flanges, packing, bolt, nuts ect. Our factory specialized in providing forged steel spare parts in raw materil, semi-finished or finished manching. The forged materil we manufactured like A105, LF2, F11, F22, F91, F92, F53, 12Cr1MoV etc. Valve spare parts material pressure ranging from ANSI classes 150 to classes 4500. The sizes of valve spare parts according to the requirements of the custmer. Our factory valve spare parts serviced numbers of state-owned EPC contractor, valve factory or project owner, even exported to Europen, USA in last five years.
Valve Spare Parts,Float Ball Valve Spare Parts,Gate Valve Spare Parts,Ball Valve Spare Parts
Yongjia South Trading Co.,Ltd , https://www.n-lvalve.com