Gas chromatography is a new type of separation and analysis method that has been rapidly developed in the past 20 years and has gradually become a specialized scientific gas chromatography method. It was first used in the separation and analysis of petroleum products. It has been widely used in scientific research and production of petroleum, chemical, organic synthesis, medicine and food industries. Not only gas chromatography but also biochemistry, clinical diagnosis and In terms of pharmacology and other aspects, especially in environmental protection, gas chromatography has become an important means for monitoring water and air. To obtain stable and reliable analytical data, it is necessary to ensure the optimal operation of the gas chromatograph system, and the performance of each part of the device such as carrier gas, inlet, column, detector, etc. greatly affects the chromatogram. The health of the system. It is important to choose a good analytical method, but the first condition is to achieve it on a stable, well-functioning chromatographic system, so ensuring the performance of each part of the device is a prerequisite for obtaining reliable analytical data.
1, carrier gas
In gas chromatography, the purity of various gases, such as carrier gas, gas, and combustion gas, directly affects the sensitivity, stability, and even the lifetime of the column (the column efficiency is 1/10 of the original, it should be replaced with new ones). Column). Therefore, the quality of the gas and the removal of impurities must be strictly controlled. Plastic pipes or rubber pipes cannot be used for the gas pipeline.
1.1 Quality requirements: The purity should be greater than 99.999%, and the FID and TCD can be greater than 99.999%. In addition, if the cylinder is used, it should be noted that when the pressure in the bottle is less than 3~5, the cylinder should be replaced because the impurities in the bottom of the bottle are high, which makes the background value of the chromatograph high.
1.2 Moisture: For capillary columns, it must be dried. It is not recommended to use water samples, even if thick film is not recommended. Because water can hydrolyze certain stationary phases, destroying the column, producing noise, tailing peaks, or ghost peaks.
1.3 Oxygen: Oxygen is the natural enemy of all capillary columns. Long-term exposure to oxygen at room temperature or near room temperature does not damage the column. However, when the column temperature rises, serious damage will occur.
In view of the above factors, in the gas chromatography system, the gas must undergo strict purification. However, you should pay attention to some tips when installing, otherwise you will not achieve the expected results. Whether it is series, parallel or hybrid, the purifier should be close to the instrument, first install the drying tube, then install the deoxidizing tube. Flush the filter (without the chromatograph) when installing or replacing the air supply for the first time. For the deoxidation tube, the carrier gas should be passed first, and the other port should be opened. Different carrier gases have different effects, which should be considered from three aspects: peak shape expansion (related to the molecular weight and flow rate of the carrier gas, large molecular weight, high column efficiency), column pressure drop (related to the viscosity of the carrier gas), detection Sensitivity (the effect of thermal conductivity on the thermal conductivity cell). Generally, the choice is as follows: when the carrier gas adopts low line speed, nitrogen should be used as carrier gas; for high line speed, hydrogen should be used as carrier gas; when pressure is large, hydrogen should be used. In addition, the carrier gas flow rate also has a certain influence on the column efficiency of the column. According to the formula u=L/t0, the optimum flow rate is determined through experiments.
2, the inlet
The function of the inlet is to accurately and reproducibly introduce the sample into the chromatographic system. The vaporized sample should be a real representative of the liquid sample. If there is no special need, the sample components of the gasification process will not undergo chemical changes. Therefore, all components that affect the gasification and stability of the sample should consider the optimum performance of each component. The part mainly has a septum, a gasket and a liner.
2.1 Septum: The function of the septum is to ensure that the sample flow path is separated from the outside, maintain the internal pressure of the system, prevent leakage, avoid external air infiltration, and contaminate the system. It is generally made of silicone rubber with high temperature resistance and good air tightness. The quality of the different types of septum is also very different, which is expressed as the number of ghost peaks and puncture resistance.
In order to avoid problems, the temperature of the gasification chamber should be controlled within the maximum temperature range; regular replacement (in order to prevent gas leakage, decomposition, sample loss, column flow or split flow, ghost peak, column efficiency) "Hand tight" after installation; use septum purge if applicable; use autosampler; use sharp-pointed syringe.
2.2 Seal: The gasket is used to seal the column or liner to the chromatographic system. It should provide a leak-free sealing effect, a suitable inner diameter, and a high temperature resistance. Improper use of the component or the use of an old gasket can result in inconsistent peaks and unreliable results. The use of improper gaskets can cause air and other contaminants to penetrate the chromatographic system, severely affecting efficiency and detector performance. To maintain optimal instrument performance, replace the seals each time the column is replaced or the column is serviced. In addition, the gasket should be dried before use to keep it clean and avoid various kinds of pollution, such as hand and oil. Re-use the gasket, pay attention to whether the gasket is damaged. There may still be some problems with replacing the gasket.
2.3 Lining: The liner is the central component of the injection system where the sample is volatilized into a gas. Choosing the right liner for different applications is a difficult and complicated task. It is also a critical step. If it is not properly selected, the following phenomena may occur: peak shape deterioration, solute discrimination, poor analytical reproducibility, and sample decomposition. Ghost peaks. Therefore, three characteristics of the liner must be considered for each application:
(1) Liner volume: The volume of the liner and the volume at which the sample evaporates are extremely important factors in the proper selection of the liner. If the liner is too small, the sample will flash back and lose, affecting the accuracy, repeatability and sensitivity of the test. In actual work, it can be calculated according to the solvent expansion formula: microliter = 22.400 × A × B × C. Where: A - density / molecular weight; B - 15 / (15 column pre-pressure psi); C - (inlet temperature 273) / 273; (for example: 1 μL of water, 250 ° C, 15 psi column front pressure 22.400 × 1 /18×15/30×523/273=1.192μL)
(2) Treatment or deactivation of the liner: There is a reactive group on the inner wall of the liner, which adsorbs the sample components, and a tailing peak appears on the spectrum, and the detection sensitivity and reproducibility decrease. The deactivated liner prevents adsorption of the sample and minimizes degradation of the labile compound. Undeactivated liners are not suitable for polar or easily degradable samples. The liner that is deactivated during the actual application process may also reproduce the activity. Although the cleaning process can be used to clean out the particles or wash the volatile components with a solvent, it is difficult and complicated to find a clean treatment method. Work, and some solvents can also remove the activation layer, and the tools used may also scratch the surface of the liner, which may result in unnecessary activation points.
(3) Types of liners: Agilent designs different types of liners for different applications. A tapered liner collects the sample on the column head and reduces sample backlash. Filled with glass wool (deactivated), in the middle of the liner: can provide more surface area, completely volatilize the sample, reduce heat unevenness, trap spacer fragments and non-volatile components to prevent these substances from entering the chromatogram Column, wipe the sample of the injection needle to prevent the sample from remaining on the septum, increasing the analytical reproducibility; at the bottom of the liner: the main purpose is to capture non-volatile components. The glass cup is mainly used to help the sample to evaporate and mix. If glass wool and inert filler are added, the analytical reproducibility can be improved and the sample discrimination can be reduced. However, glass wool liners are not suitable for the analysis of phenols, organic acids, pesticides, amines, reactive polar compounds, and thermally labile compounds. Liners for split/splitless have good benefits for samples with complex compositions.
All of the above three characteristics can affect the gasification of the carrier gas flow through the inlet or sample, and the effects of these factors should be considered in practical applications.
3, detector
Most detectors are general-purpose, such as FID, TCD, etc., as well as detectors for special substances such as ECD, NPD, etc. There are different requirements for different detectors. Some major detectors are now being explored.
3.1, FID FID (hydrogen flame detector) has high sensitivity, small dead volume, fast response, wide linear range, and can be effectively combined with capillary column, which has become the most widely used detector for microanalysis of organic matter. The FID detection system is mainly composed of three parts: detector, detection circuit (amplifier) ​​and gas path. When a fault occurs or the analysis spectrum is abnormal, it should first be judged which part is the difference. Common abnormalities in FID systems are: no ignition, the problem is mainly in the gas path or detector; the base flow is very large, the problem is mainly in the gas path or detector; the noise is very large, the gas path, the detector and the circuit are all problematic. It is possible that the sensitivity is significantly reduced, the gas path, the detector and the circuit are abnormal; the peak, the gas path, the detector, and the circuit are not normal; the peak shape of the chromatogram is abnormal: the sampler, the gas path, The detector is the main inspection object; the baseline drift is serious, the gas path and the detector are possible; the burr, the collector and the nozzle are unclean. Common detection steps:
(1) Check the gas path and check whether the flow rate of H2 (hydrogen), N2 (nitrogen), AIR (air) is normal, the air flow rate is too small, and the nozzle is seriously leaked, which will cause a large popping sound and cannot be ignited; Small, too large nitrogen will make ignition difficult and easy to extinguish; nozzle leakage, column leakage will not only make ignition difficult, but also lead to reduced sensitivity, or even peak; hydrogen to nitrogen flow ratio will significantly affect sensitivity; hydrogen flow too Large can also cause loud noise; the gas path system is not clean, including injector contamination, detector contamination, or insufficient aging of the column can cause base flow, loud noise, and baseline drift. Please pay attention to the size of the base flow during ignition: Before the ignition, the baseline position of the detector should be zero or very small, only about 0.1~0.3. When the H2 gas is returned to the normal working value after ignition, the baseline is within 100. , indicating that the system is very clean, generally can be used; if the baseline value is large, it means that the system pollution is more serious, then the noise and drift are very large, and the instrument stabilization time is also longer. A simple way to check which part is contaminated is to separately increase the operating temperature of a certain part. If the baseline becomes significantly larger, the part is seriously polluted. Blockages and leaks in the gas path (including the injector) tend to cause abnormal peaks; the flattening of the liner in the injector also destroys the normal peak shape.
(2) Check the detector to check if the nozzle is leaking or blocked. In addition, it should also be noted that stagnant water, filament aging, and rust are also a cause of no fire. In addition, for the use of the detector, the temperature setting should be no less than 150 ° C, it is recommended to be above 200 ° C, and should be ignited at this temperature for a certain time, so that the moisture remaining in the detector can be removed, and can be turned off first when closed. Hydrogen, continue to open the air, to avoid the adhesion of some impurities.
(3) The nozzle and collector of the detector should be cleaned as follows: solvent ultrasonic-hot water washing-methanol washing-drying. Remember that it is not possible to scratch the nozzle or collector with a sharp hard object, which will result in a new activation point. When installing, remember not to touch the part directly with your hands.
3.2. TCD For this detector, it must be ensured that the carrier gas, the reference gas and the makeup gas are from the same gas source; the reference gas is cleaned and the temperature is over 150 °C to open the filament. The detector should be cleaned and cleaned for several hours before cooling to normal operating temperature. When cleaning, disconnect from the column and plug the connection to the column.
3.3. ECD Since the detector has a radioactive source, the exhaust gas should be discharged to the outside. When cleaning, do not remove the detector, only hot cleaning, heating to 375 ° C, the tail gas is 50 ~ 60mL / min.
3.4. NPD The detector is mainly used to detect nitrogen and phosphorus, which is basically the same as FID. The difference is that there are beads on the top of the nozzle. Therefore, special attention should be paid to heating and drying because of the fear of moisture when not in use for a long time. Cleaning should also be done by hot cleaning. In addition, the injection technology is also a big factor. Do not take the needle of the syringe and the sample part when injecting, do not have air bubbles; slow and fast discharge when sucking the sample, then slowly suck, repeated several times, the volume of the metal needle part of the 10μL syringe is 0.6μL, it is difficult to observe the bubble, suck more 1~2μL push the tip of the syringe up, wait for the bubble to move to the top and push the syringe to remove the air bubbles. The injection speed is fast (but not too fast) and the same speed is maintained for each injection. However, in actual work, it often occurs to ensure the injection speed, and the syringe needle and the syringe rod are often bent, because:
(1) The injection port is too tight, and the screw is too tight at room temperature. When the temperature of the gasification chamber rises, the silicone gasket will be tighter after expansion;
(2) The position error needle is tied to the metal part of the inlet;
(3) The force is too strong when injecting;
(4) There is contamination on the inner wall of the syringe. When the needle is pushed and bent during injection, the syringe will find a small black piece near the top of the needle for a period of time. At this time, the injection is difficult. Cleaning method: Pull out the needle bar, inject a little soapy water, and push and pull the needle bar repeatedly. This will help, but clean the syringe. When the sample to be analyzed is a solvent-dissolved solid sample, the syringe should be cleaned with a solvent in time after injection.
(5) Be sure to keep it steady when injecting, otherwise the syringe will be bent.
In general, the influencing factors of anything are diverse, as is the case with gas chromatography. Therefore, in practice, corresponding solutions should be taken for different reasons.
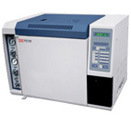
Entry lockset is one of our main door lock product range in Gumei Lock, with three different specification in size -- small, medium and large. Facing various market demand, Gumei Lock has developed two materials for main door entry lockset: Zinc-alloy and Aluminum. Please contact us for more information and get the lastest price for all of lock in keyed.
handleset locks, lock in keyed, main door lock, entry set lock, entry lockset
ZHONGSHAN JUYA METAL PRODUCTS CO., LTD , https://www.gumeilock.com